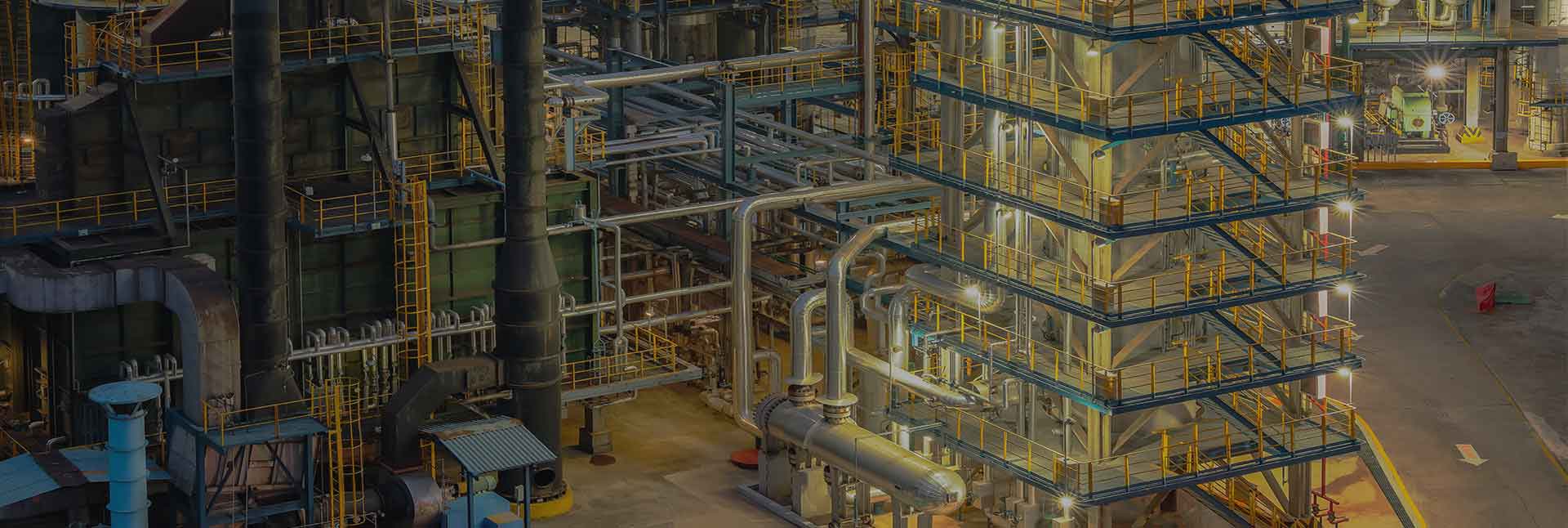
把握宏观脉络 洞悉行业趋势
GRASP THE MACRO CONTEXT INSIGHT INTO INDUSTRY TRENDS
球面滚子技术工艺发展趋势分析(球面滚子项目市场投资商业计划书 -节选)
第一节 产品技术发展现状
1、FAG轴承与INA合作研发新一代E1球面滚子轴承
FAG轴承公司又制定了新一代的球面滚子轴承标准-E1。新标准下的轴承性能更佳,能耗更低,运行稳定性更好。新轴承在负载能力上比原先产品提高了17%,这样轴承寿命可以延长到原先标准的1.7倍,更重要的是性能提升的同时产品的性价比同样得到了提升。
可以在性能上获得如此的提高全靠近期在轴承运动学、材料学和制作流程上一些重要突破。表现极佳的E系列设计(E系列设计指去除了轴承内圈上的中心槽(centerlip),这样可以放入更多高负载力的圆柱滚子),FAG的设计师从几何学的角度对轴承和滚子所作的特别优化。动态负载率的提高使轴承可以承受更大的负载。所有这些提高使得新一代轴承的性价比更高。现在顾客选择的余地很大,既可以选用原尺寸高性能的产品,也可以选择小尺寸但性能和上一代产品相同的E1系列轴承。总之,E1系列轴承与上一代产品相比具有更高的效率。据说,E1的下一代产品将会带给用户更高的性价比。
高性能和长寿命是FAG和INA所创造的X-Life理念的核心内容。所有新一代轴承出场前都要经过严格的各项指数评测,只有合格产品才能流入市场。
E1系列球面滚子轴承型号齐全,从20mm内径到320mm外径总共有8个系列。这使得E1能胜任高速或高负载等各种工作。而且E1还分圆柱和圆锥结构,使它的适用性更强。
2、瑞典SKF突破球面滚子轴承技术难点
SKF新近研制的Explorer球面滚子轴承更加增强了其霸主地位。
Explorer球面滚子轴承的使用寿命与标准的相同尺寸的球面滚子轴承相比提高了300%,且能够承受高于25%以上的扭矩负荷。Ex-plorer轴承在较低的温度下运转得更快,噪音更小,振动更小,并且耐受污染。这些性能的变化不仅仅是结构的改变,而是减小宏观和微观状态下应力集中和对接触表面间的油膜厚度进行优化的结果。开发Explorer轴承的过程中,SKF的科学家对钢的晶粒微组织结构进行了 研究 ,将氧含量降至最低,从而制造洁净、均匀结构的钢。开发工程师和应用工程师通力配合确保每个轴承零件都合格,从而最大限度地发挥润滑效果,减小摩擦和磨损。
Explorer球面滚子轴承结构最显著的特点是有一个浮动导环、对称的自引导滚子(在滚子长度周围提供均匀的负荷分布)、特殊的滚子轮廓(能将边缘应力降为最小)、结实的金属保持架(可承受高温)和润滑剂。外圈上有一个环形油沟和三个进油孔。由于Explorer轴承增加了单位容量,轴承的寿命更长,可靠性更高。Explorer球面滚子轴承的开发成功为机床设计“小尺寸”或“大功率”战略目标开辟了道路。
第二节 产品工艺特点或流程
球面滚子工作面为球形,有较高的尺寸精度和表面质量要求。当球面滚子的有效直径大于20mm时,一般采用棒料直接车削成形。这是因为冷变形时轴承钢的塑性差,变形抗力急剧增加,模具材料的强度也难以承受模具的单位载荷;而热锻成形虽然变形力小,但是热锻件的尺寸精度和表面粗糙度不能满足后续加工的要求,无法直接进行磨削。另外,热锻后的退火加剧了脱碳程度和材料消耗。因此,切削成形成为国内生产直径20mm以上球面滚子的普遍加工方法。
1、切削成形工艺的特点
车削成形主要是采用仿形车床切削球面滚子的球形工作面。为了保证原材料的脱碳层和表面缺陷不致影响零件的表面质量和内部组织,车制件的外径应小于棒料直径1-2mm。一般情况下,标准的圆棒料直径很难与零件的直径相匹配,车削前还要对原材料进行拉拔,增大了加工费用。若直接采用标准直径的棒料进行车削,则棒料直径要大于零件名义直径2-4mm,再加上零件间的切缝不小于5mm,因此,切削工艺的材料利用率仅为50%-60%。此外车削工艺生产效率较低,数台车床连线班产也仅近千件。
轧制圆棒料的金属流线沿棒料轴线连续分布,球面切削成形后,使平行于轴线的金属流线被切断,在高载荷的交变应力作用下,极易在其工作表面引起疲劳剥落。
2、塑性成形工艺及特点
塑性成形工艺是通过转移金属体积来成形零件,其材料利用率大大高于切削成形,就球面滚子而言,单件平均材料利用率可提高25%-30%。
塑性成形可分为热锻、冷挤压和温锻。由于中大型球面滚子的尺寸较大,轴承钢材料的强度和硬度高,塑性较差,冷变形抗力非常大,对压力机和模具提出了更高的要求。如直径大于35mm的球面滚动体,采用4000kN曲柄压力机冷挤成形,模具寿命短,早期失效是模具报废的主要原因。
热锻时,材料的强度下降,塑性明显提高,有利于成形。但是1050-1100℃的始锻温度会在锻件表面生成较厚的氧化皮,并伴有不同程度的脱碳层,锻件的加工余量和锻造公差较大。而且锻后还必须进行球化退火,增加了能耗,也不利于精化锻件,给后面的车削加工带来了困难。若直接进行磨削,无论磨料消耗还是工时消耗等方面都是不经济的。
轴承钢的温锻温度通常是接近相变温度,此时金属材料塑性好,变形抗力低和氧化烧损少。其成形力仅为冷挤压的3/1-2/1,成形精度接近冷挤压,而且锻后无需进行退火。
根据球面滚子尺寸不同,使用的原材料主要为GCr15或GCr15SiMn钢,这两种材料均为高碳高合金钢,属过共析钢。温锻成形温度一般取700℃或700℃以下,这样可以避免800℃以上时金属发生剧烈的氧化,加热后锻件表面仅生成极微小的氧化膜。同时,因加热温度没有达到材料的相变温度,锻后仍然可得到原材料的球状珠光体组织,并且球状珠光体晶粒细化、分布均匀,为热处理淬火做了较好的组织准备。
球面滚子温锻成形有半模膛成形和模膛成形两种成形方法。所谓的半模膛成形工艺过程为:加热后的坯料镦粗后,在半敞开式的模膛内成形,利用成形时的镦粗效应形成的自然鼓形(近似于球面)作为球面滚子的工作部分。其优点是成形力低,对模具的精度要求不高,没有飞边。但缺点是成形的尺寸精度不高,球面滚子锻件的形状与零件的形状相差较大,材料利用率提高有限,并且后续的机械加工量明显增加。
模膛内成形的工艺过程为:坯料润滑处理后,经中频感应加热炉加热,闭式预成形,然后在终锻模膛内成形。整个锻件均在由凸模和凹模组成的模膛内成形,仅在锻件的最大直径处留有少量的飞边。锻件成形后将飞边切除,即可得到与零件尺寸和形状极为接近的球面滚子温锻件。其尺寸精度受温度波动的影响小,温锻件的尺寸精度接近冷挤压件,可达±0.1-0.15mm,锻后可直接进行磨削,不需要再进行任何的车削加工。这种工艺的最大特点是:材料利用率可高达90%以上,零件的内部组织致密,金属流线沿球面滚子球面工作部分连续分布。制成成品后,金属流线不会在整个工作表面露头,有利于提高滚子的耐疲劳性能。生产效率也比车削工艺高五六倍。
不同的成形工艺对后续加工工艺的要求是不同的。长期以来,国内企业对车削成形的球面滚子毛坯有一套较为成熟的后续加工工艺,而温锻调心滚子的尺寸精度和形状与车削球面滚子有一定的差别,因此温锻毛坯机械加工时,应对原来的工艺进行相应地调整。
3、温锻件的后续加工
用回归法对车削成形球面滚子和模膛成形的温锻球面滚子这两种毛坯的尺寸精度进行比较 分析 ,可以看到,车削件尺寸精度比温锻件高0.05-0.1mm,而后者的尺寸收敛性要明显优于前者,其批量产品的尺寸公差呈线性分布,更适合后续的磨削加工。车削件的尺寸敛散性大,公差范围内的尺寸呈无规律分布,会对后续工序的尺寸精度带来一定的影响,只能通过增加一道磨削工序来消除。
1)车削件的后续加工
在实际生产中,车削件的后续加工工艺为:车削件直接进行热处理淬火,回火后初磨球面,然后磨削凸端面和凹端面,最后精磨球形工作面。其中初磨球形工作面是为了消除车削后工件尺寸的敛散性,保证精磨工序的质量。但是初磨工序在热处理淬火后进行,对于磨削效率和磨料的损耗都有一定的影响。
2)温锻件的后续加工
(a)初磨工序安排在工件热处理淬火前进行。
由于温锻件的成形特点,在工件的最大截面处有工艺性飞边。其作用是在成形时形成水平阻力圈,使模膛内的金属形成强烈的三向压应力状态,有利于金属充满模膛,得到完整、饱满的锻件。成形完毕飞边切除后会在工件上留下一定的残留环带,若直接对球面进行软磨,会增加砂轮的不均匀磨损。因此在锻造工序完成后,应在无心磨床上窜磨一道,去除残留环带。无心磨床的效率非常高,软磨时对磨料的要求不高,磨料消耗较小,且能实现自动化操作,因此对温锻球面滚子的成本影响不大。
由于曲柄压力机的成形特点,温锻件的下料重量误差、温度波动误差等主要反映在工件的高度尺寸上。故温锻件的高度尺寸精度要逊于车削件,高度尺寸公差要比后者大0.1-0.15mm。在淬火前还应增加一道双端面磨削,以提高工件高度的尺寸精度。与无心窜磨一样,双端面磨削也采用通用机床,效率较高,磨料消耗少。
前两道工序完成后,在淬火前还要进行一道初磨工序,即软磨球形工作面。该工序实际上是将原车削件淬火后进行的初磨工序改为温锻件的软磨工序。其作用是磨去工件精磨前的余量,为淬火后的精磨工序作准备。软磨后的尺寸为零件尺寸加上精磨余量。精磨余量的大小应保证能去除淬火后新增的脱碳层。
温锻件的磨削工序
(b)淬火后的加工工序。
由于温锻件的初磨工序基本保证了精磨工序的坯料质量,因此球面滚子淬火后的精磨工序要比车削件磨削量少,减少了一道球形工作面的初磨工序。精磨效率也有一定幅度的提高。其余的工序等同于车削成形球面滚子的加工,即磨凹端面和凸端面。
综合两种工艺的后续加工特点和加工量可以看到:温锻件的后续加工仅增加了窜磨环带和双端面磨削两道初磨工序,而这两道工序安排在淬火前进行,又采用通用设备,自动化程度和生产效率都较高,对温锻滚动体成本的影响有限。
4、结论
采用温锻成形工艺取代车削成形工艺生产轴承球面滚子,可以使材料利用率提高近30%左右,生产效率也提高了近五六倍。而且可以使零件的内部组织更加致密,力学性能得到相应提高。对于实现轴承滚子的精密成形和提高经济效益都有积极作用,具有广泛的推广价值。
第三节 国内外技术未来发展趋势 分析
新的球面滚子技术的发展将趋于高精、高效、柔性及自动化方向。
1、开展实用的、低成本、高效率的制造技术 研究 。当前的球面滚子制造或多或少的都存在着制造成本高、效率低、装置复杂、操作不易掌握等局限性,所以开发低成本、高效率、适应性广、工业化应用程度高的球面滚子技术已成当务之急。
2、开发球面滚子的在线检测、监控、故障自诊断技术。利用声信号来判断工况,对滚轮质量进行评估,应用计算机对制造过程进行控制,开发检测、处理、质量评估、控制一体化的制造系统。
3、应用自适应控制技术和专家系统技术、实现滚子的智能化制造。模糊数学、数据库、以范例和模型为基础的决策系统、专家系统等理论与技术的发展及其在制造业中的成功应用,为球面滚子技术的智能化提供了可靠的技术基础。
4、开发远程控制系统。应用网络技术对制造过程进行远程操作、管理、临控与诊断。
免责申明:本文仅为中经纵横 市场 研究 观点,不代表其他任何投资依据或执行标准等相关行为。如有其他问题,敬请来电垂询:4008099707。特此说明。
您的需求
YOUR REQUIREMENTS
咨询热线:
400-8790-365 400-8099-707
服务邮箱:vip@jihuashu.org.cn
单位官网: http://www.jihuashu.org.cn
地址(北京):北京朝阳区光华路东方梅地亚中心A座15层
地址(上海):上海杨浦区军工路1599号1栋5层
ICP 备案:沪ICP备18002139号-5
主营业务
- 报告编制
- 可行性报告
- 商业计划书
- 项目建议书
- 立项申请报告
- 稳评报告
- 能评报告
- 项目方案
- IPO募投可研
- 项目申请报告
- 企业融资报告
- 规划设计
- 乡村振兴规划
- 特色小镇规划
- 产业规划
- 文化旅游
- 十四五规划
- 园区规划
- 田园综合体
- 乡村旅游
- 康养产业
- 景观设计
- 科技成果评价
- 科技成果评价
- 项目立项评估
- 项目结题评价
- 知识产权评估
- 成果价值评估
- 人才团队评价
- 扶持资金申请
- 农业资金申请
- 发改委资金申请
- 工信资金申请
- 科技资金申请
- 网站地图
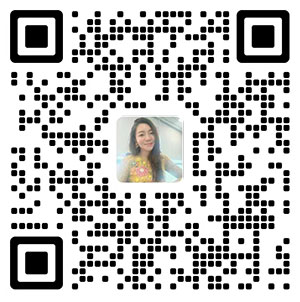
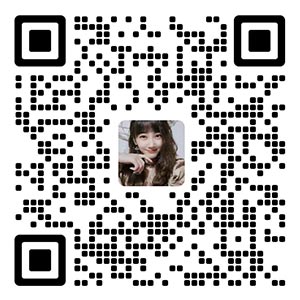